The electric car world, which has made a name for itself quite frequently, has once again taken a big step forward. This time not with the launch of a new model, but with a breakthrough related to the change in production techniques.
Tesla’s “gigacasting” Its latest successes in the field have already impressed its competitors and enabled them to follow the path taken by the American electric vehicle giant. Tesla has effectively redesigned the production of the Model Y’s front and rear structures with its mega-presses applying between 6,000 and 9,000 tons of clamping pressure. This process has greatly reduced costs, far surpassing traditional production methods.
Announced by Musk earlier this year “without box” The production strategy is poised to take this one step further. So what’s the point here? Mold nearly the entire complex underbody of an electric vehicle as a single piece. In comparison, a conventional car uses approximately 400 parts. Imagine: 400 parts reduced to just one.
Now, “What’s the big deal?” you may be wondering. Let’s take a look at the statement made by Terry Woychowski, president of the US engineering company Caresoft Global: Covering a large part of the lower body of an electric vehicle with Gigacasting will revolutionize automobile design and production. Woychowski, a veteran who worked at GM for more than thirty years, “This is a game changer” says. However, “Casts, especially at this scale and complexity, are incredibly difficult.” he adds.
It is said that Tesla’s unique design and manufacturing approach can reduce the development time of a car to just 18 to 24 months. To illustrate this with an example, a factory producing cars by traditional means typically needs three to four years.
So what do all these innovations mean for the consumer? In fact, the biggest impact for us consumers is the possibility of having more affordable electric vehicles. Another advantage is that larger areas can be created for the positioning of batteries. In this way, more batteries can be used for longer range.
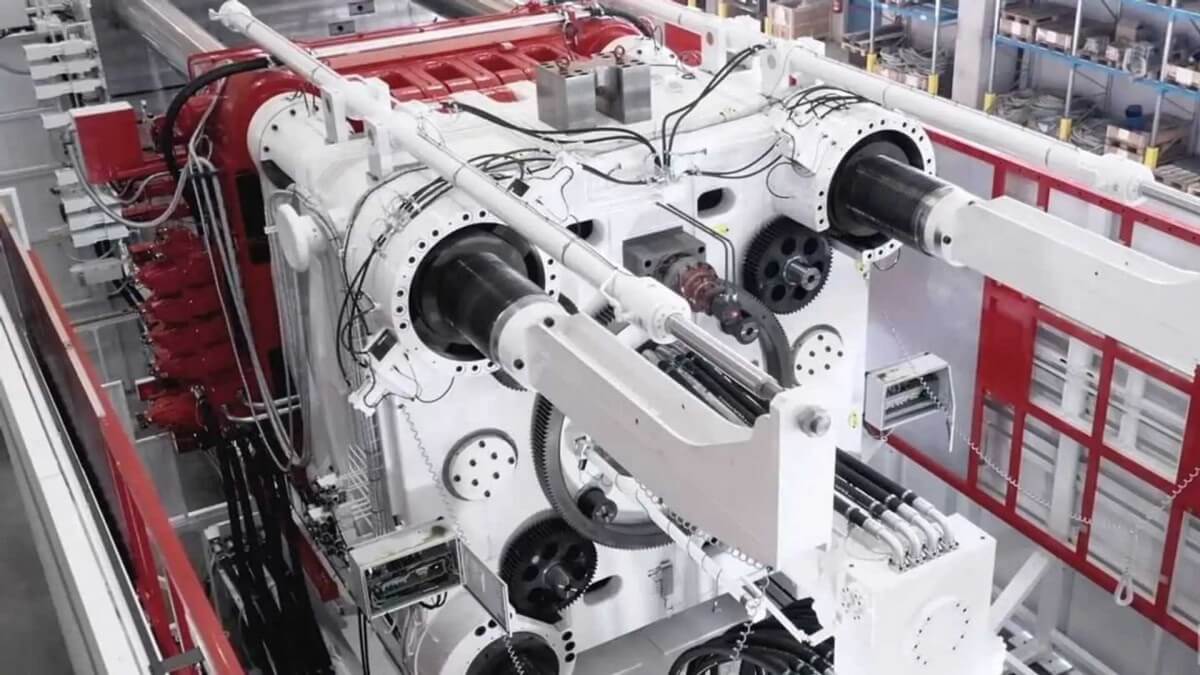
But here’s where things get even more exciting (if that’s even possible): the real innovation lies in the mold-making process. Traditionally, automakers “gigacast dilemma” They stayed away from huge structures because of this: You can think of this as high costs, multiple risks and exorbitant expenses when fine-tuning is required.
Tesla’s solution? 3D printing using industrial sand. With this method, even with several iterations, the cost of the verification process is only a fraction of that of metal prototypes. But every story has risks and wrinkles. Despite advances in mold design, Tesla had to overcome the difficulties of casting aluminum alloys. The different behaviors in sand and metal molds often fell short of Tesla’s quality criteria. What’s the solution? Special alloys, refined cooling processes and post-production heat treatments.
Interestingly, Tesla’s upcoming small car could be a test bed for this monolithic EV platform approach. It is an ideal candidate given its simpler design.
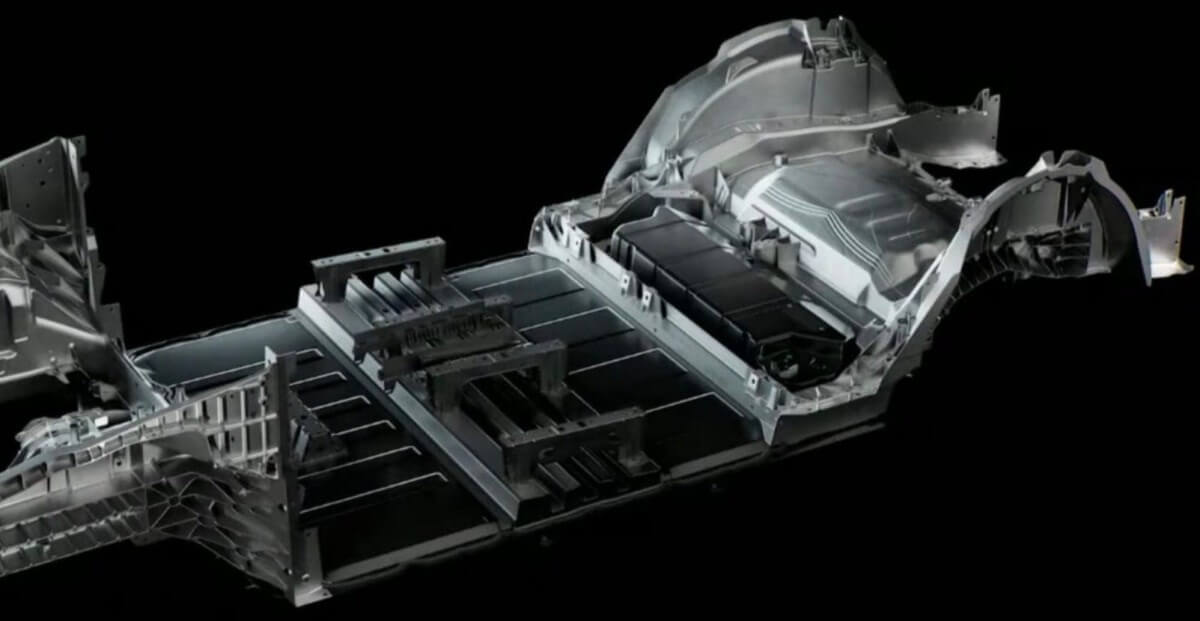
However, the journey is not entirely smooth. Tesla has not yet finalized the type of press he will use for this job. A press with high clamping force can quickly produce large body parts but may not accommodate the 3D printed sand cores that are crucial for hollow subframes. There’s a balance between speed and quality – which path will Tesla choose? We will wait and see together.