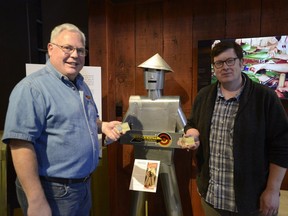
No one thought they could do it.
Advertisement 2
Article content
Article content
Recommended Videos
Article content
A farm machinery company making precision aircraft parts? No luck.
“They were considered forgers of crude iron up to that point,” said Rob Adlam of the Brantford-based Canadian Industrial Heritage Centre.
“There’s a world of difference between making a hand plow and making aircraft components,” Adlam said. “The government even had doubts they could do it.”
But wartime calls for creativity, and Cockshutt Plow Company in Brantford — best known for making tractors and harvesters — rose to the opportunity to get Allied planes into the sky to take on Nazi Germany.
From inside a million-dollar factory on Greenwich Street — built in just three months in 1943 — Cockshutt’s newly formed aircraft division turned out landing gear for the Lancaster bomber, targeting components for the B-29 Superfortress bomber, and fuselages for the Mosquito, a speedy, lightweight fighter made of laminated plywood.
Advertisement 3
Article content
Pilots at Commonwealth air force training bases across Canada — including in Jarvis and Dunnville in Haldimand County — learned to fly inside the Avro Anson, whose exhaust manifolds were made by Cockshutt’s wartime workforce.
“No implement manufacturer had ever attempted any of that,” Adlam said. “But they proved that they could do it.”
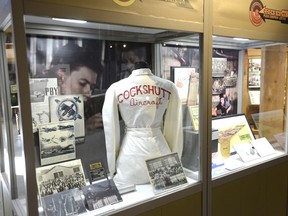
The work had to be precise, since Cockshutt was one of 39 subcontractors making parts that were shipped to a factory in Malton for assembly.
“Thirty-nine different groups making these different components and putting them all together — and this was before computers,” said James Christison, curator of the Waterford Heritage and Agricultural Museum.
“It’s amazing all the holes lined up,” Adlam added.
Advertisement 4
Article content
Adlam and Christison led The Spectator on a tour of “Swords and Plowshares Revisited,” an exhibit on at the Waterford museum until the end of February that explores what Christison calls “the battle on the industrial front fought by the women and men in the nation’s factories.”
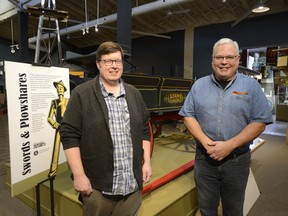
Like their competitors, Cockshutt was forced to cut production of farm equipment by 75 per cent during the Second World War because the military needed the rubber and steel for the war effort.
Instead, the company’s 6,000-strong workforce — a “huge percentage” of them women, Adlam noted — made hand grenades, submachine guns, bullets, artillery shells, army truck bodies, ambulances, portable bridges, and tank parts intended for battlefields around the world.
Advertisement 5
Article content
“What kept them afloat was war contracts,” Adlam said.
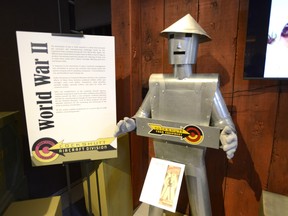
History of wartime service
Cockshutt’s pioneering aviation efforts continued a tradition of wartime service from one of Brantford’s major employers and the family that owned the company.
Through persistent petitioning of his bosses in Ottawa, WF Cockshutt, Brantford’s member of Parliament during the First World War, got permission to form a Brantford-Brant battalion and recruited 1,100 new troops that went overseas in July 1916.
In the meantime, company president Harry Cockshutt — known as an energetic and community-minded businessman — poured his personal wealth into raising the 215th Battalion.
Colonel Cockshutt, as he became known, paid to train new recruits before they were shipped off to Europe with 30 transport wagons and a field hospital also personally funded by Cockshutt.
Advertisement 6
Article content
The elder Cockshutts were motivated by “a high sense of patriotism,” Adlam said.
“They weren’t happy to sit back and let others go perform their duty for them. They got personally involved,” he said.
The exhibit at the Waterford museum includes medals, insignia badges, weapons, duffel bags and documents from Cockshutt relating to war, with many artifacts donated by the family and on public display for the first time.
A sheathed bayonet once belonging to future company president Capt. Charles Gordon Cockshutt — a cavalry soldier awarded the Military Cross for battlefield valor — hints at a close call.
The top of the sheath has a bullet hole, and the bayonet itself is bent in the same spot.
“A bullet hit the sheath and the blade stopped it,” Adlam said. “It’s an interesting story that you wish someone was around to tell and fill in the blanks.”
Advertisement 7
Article content
The exhibit’s “showstopper” is a meticulously restored Adams wagon, an Ontario farm wagon built in Brantford in 1919. The wooden wagons were used to move farm supplies and livestock and to build and maintain municipal roads.
During the First World War, a Cockshutt subsidiary made thousands of Adams wagons that were sent overseas by boat to be assembled and used for troop and supply transport, with “dump wagons” fitted with doors that opened to release dirt and rocks while building roads over destroyed terrain.
The Adams wagon on display in Waterford was found disassembled in a farm shed in the Onondaga area and purchased by a collector who restored it and later sold it to Adlam.
“In its condition, it’s pretty rare,” Christison said. “There’s not too many of these around.”
Advertisement 8
Article content
That wagon was not shipped overseas, Adlam clarified.
“I’m sure anything that went to Europe never came back,” he said. “It either stayed there or was blown to pieces.”
The rarity of seeing an intact Adams wagon and a Cockshutt-made exhaust manifold from an Anson training aircraft, alongside personal artifacts from the family’s private collection, have brought Cockshutt enthusiasts to the museum in droves.
“We’ve had people from all over the country come to see (the exhibit),” Christison said. “There’s such an interest in the Cockshutt company.”
Cockshutt kept up some military contracts into the Cold War, making custom forklifts for the air force and specialized trailers to house radar equipment while publishing pamphlets warning employees “against the insidious effects of communism.”
The company’s aircraft division made jet engine parts for the ill-fated Avro Arrow, a supersonic fighter jet canceled in 1959 by the Diefenbaker government.
“These are the little-known stories that we’re trying to bring together,” Adlam said.
JP Antonacci is a Local Journalism Initiative Reporter based at the Hamilton Spectator. The initiative is funded by the Government of Canada.
Article content