Der 3D-Druck von Objekten aus Metall ist eine gut etablierte Technik, die jedoch tendenziell zu komplex, teuer oder ungenau ist, um mit herkömmlichen Methoden in großem Maßstab mithalten zu können. Ausgestattet mit 14 Millionen US-Dollar von Nvidia und Boeing, Freiform will das ändern, indem es ein neues additives Metalldruckverfahren entwickelt, von dem es heißt, dass es die Spielregeln verändert – und ja, es gibt auch einen KI-Aspekt.
Die Mitbegründer Erik Palitsch (CEO) und TJ Ronacher (Präsident) arbeiteten beide bei SpaceX, wo sie als Hauptarchitekten bzw. leitende Analysten der Merlin-Triebwerke und anderer Programme fungierten. Dort erkannten sie das Potenzial des 3D-Drucks von Teilen aus Metall, erlebten aber auch die Mängel der Methode aus erster Hand.
„Wir haben das Potenzial des Metalldrucks erkannt; Es hat das Potenzial, praktisch jede Branche zu verändern, die Metallgegenstände herstellt. Aber die Akzeptanz verlief langsam und der Erfolg war bestenfalls marginal“, sagte Palitsch. „Warum ist der Einsatz im großen Maßstab nicht praktikabel? Im Wesentlichen aus drei Gründen: schlechte und inkonsistente Qualität; Geschwindigkeit – kommerzielle Drucker sind sehr langsam; und Kosten – der Preis für diese Drucker ist astronomisch.“
Sie kamen zu dem Schluss, dass sie die ganze Sache aufdecken könnten, wenn sie den Prozess so umsetzen könnten, dass sie einen Druckdienst anbieten, anstatt einen Drucker zu verkaufen. Also schlossen sie sich mit Tasso Lappas, dem ehemaligen CTO von Velo3D, zusammen, um Freeform zu starten.
Der Hauptfehler, den die Unternehmen machten, bestand darin, CNC-Maschinen, die üblicherweise in der traditionellen Fertigung eingesetzt werden, als Modell für die Metalldruckerei zu verwenden. In diesem Fall verkaufen Sie die Maschine und ihre Software und sorgen dafür, dass sie mit den von Ihnen verwendeten Formen und Verfahren funktioniert. Aber Metalladditive seien anders, sagte Palitsch.
„Die Art und Weise, wie diese Dinge heute funktionieren, ist eine ‚offene Schleife‘ – sie spielen im Grunde eine Datei ab“, erklärte er. „Sie mussten intelligenter sein, denn der Prozess, bei dem man Metallpulver mit einem Laser schmilzt, ist äußerst kompliziert und in gewisser Weise stufenlos variabel.“
Den Leuten eine Maschine zu verkaufen und zu sagen: „Werde ein Experte, damit sie funktioniert, viel Glück“ ist kein Erfolgsrezept.
„Aber wenn man beschließt, keinen Drucker zu bauen und in einen Karton zu verpacken, wenn man die Freiheit hat, eine automatisierte Fabrik von Grund auf aufzubauen, kann man viel tun“, sagte Palitsch.
Ihre Lösung besteht darin, Drucken als Dienstleistung mithilfe eines geschlossenen Prozesses in einer maßgeschneiderten Maschine bereitzustellen, die den Druck im Mikrosekundenbereich überwacht und verschiedene Faktoren anpasst, um die Art von Druck zu erzielen, die an einem Arbeitsplatz wie SpaceX erwartet wird.
Das Unternehmen kann sich zahlreicher technischer Fortschritte rühmen, aber die beiden unmittelbar relevantesten sind die Feedbackschleife und die KI, die sie verwaltet.
„Wir verfügen über Hochgeschwindigkeits-Computer-Vision-Feedback auf unserem System, das im Mikrosekundenbereich läuft, und alle diese Daten werden auf hochmodernen FPGAs und GPUs verarbeitet. Wir mussten diesen gesamten Stack selbst aus Dingen aufbauen, die erst in den letzten Jahren verfügbar geworden sind“, sagte Palitsch.
Das geschlossene System mit Echtzeitüberwachung mildert Qualitätsprobleme und ermöglicht dennoch das schnelle Drucken komplexer Geometrien. Und indem sie als Druckdienstleister agieren, halten sie das Geschäftsmodell einfach.
Damit dieser Teil des Systems funktioniert, war jedoch der zweite technische Durchbruch erforderlich: ein maschinelles Lernmodell, das schnell genug und kompetent genug ist, um diese Überwachung tatsächlich durchzuführen.
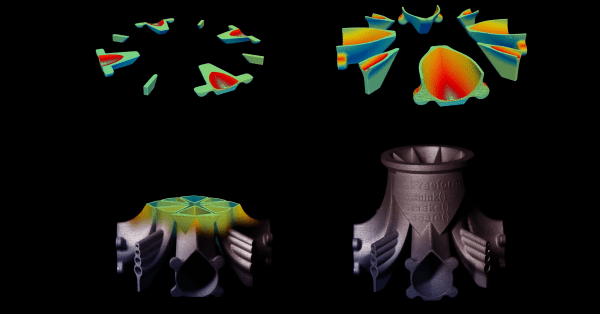
„Erik und TJ haben das erlebt und sind zu dem gleichen Schluss gekommen, dass diese Branche ein Maß an Rechenleistung und Sensoren erfordert, das noch nie zuvor jemand eingesetzt hat“, sagte Lappas.
„Um richtig zu verstehen, wie der Prozess gesteuert werden kann, brauchten wir Datensätze, die in Zeiträumen funktionieren, die niemand hatte. Also begannen wir mit dem Aufbau eines hochmodernen Telemetriesystems, einer Plattform, die kuratierte, kontrollierte, fast selbstbeschriftete Datensätze sammelt.“
Mithilfe dieser Daten konnten sie ein Modell booten, um mehr Daten für ein besseres Modell zu generieren und so weiter.
Doch dann gerieten sie in die Notwendigkeit der Geschwindigkeit.
„Wir haben viele Gemeinsamkeiten mit generativen Modellen, aber auch vieles nicht. Aber was völlig anders ist, ist die Latenz“, erklärte Lappas. „Unsere Schlussfolgerung muss in Mikrosekunden erfolgen, damit wir den Kreis dieser Prozesse schließen können.“ Da für die Daten oder die Rechenleistung keine Standardlösung verfügbar war, mussten sie die GPU/FPGA-Kombination „KI auf Steroiden“ von Grund auf neu entwickeln.
Ein daraus resultierender Nebeneffekt: Freeform „baut den größten Metalladditiv-Datensatz der Welt auf – deshalb kommen Unternehmen wie Boeing zu uns“, sagte Palitsch. „Wir verfügen über diese grundlegende Fähigkeit zur Datenerfassung und -verarbeitung, die sonst niemand hat.“
Zusammen mit den grundlegenden Vorteilen der druckbasierten Fertigung, wie der Agilität und Vielseitigkeit von Fabriken, ergibt sich ein ziemlich überzeugendes Geschäftsmodell.
Boeings AE Ventures und Nvidia investierten insgesamt 14 Millionen US-Dollar, lehnten jedoch eine weitere Aufschlüsselung ab. Die Investition jedes Unternehmens bringt Vorteile mit sich: Nvidia gewährt ihnen Zugang zu H100s und anderer Computerhardware, während Boeing sie durch den Lieferantenqualifizierungsprozess begleitet und wahrscheinlich eine Reihe von Teilen kauft. (Freeform wird auch dem Inception-Startup-Programm von Nvidia beitreten.)
Palitsch sagte, sie hätten Kunden in den Bereichen Luft- und Raumfahrt, Automobil, Industrie und Energie, „alle neun“. Sie lehnten es ab, etwas zu dokumentieren, erwähnten jedoch, dass sie alles herstellen, von Komponenten für Raketentriebwerke bis hin zu Auspuffteilen für Formel-1-Autos. Mit dem Geld wollen sie expandieren, ihre nächste Generation von (viel schnelleren) Druckern entwickeln und im Laufe des nächsten Jahres insgesamt bis zu 55 Mitarbeiter einstellen.
Er räumte ein, dass ihr Ansatz Zeit brauchte, um von der Theorie zur Realität zu gelangen, dass aber auch ihr methodischer, technischer Ansatz den Erfolg ermöglichte.
„Es war ein langsamer Übergang“, sagte Palitch. „Aber wenn ich zurückblicke, haben wir mit sechs Leuten von Grund auf die schnellste Laserschmelzplattform der Welt sowie die Hardware und Software dafür gebaut. Wir haben Dinge getan, von denen die Leute sagten, dass man sie nicht tun könne.“