Intel hat uns zu einem besonderen Besuch eingeladen fortschrittliche ChipverpackungMontage- und Testeinrichtungen auf der Insel Penangund ein weiteres in der Festlandstadt KulimMalaysia und es war ein wirkliches Erlebnis.
Während der Tour haben wir zwei Einrichtungen besichtigt. Der Montage und Test in Penang In der PGAT-Anlage werden die Siliziumchips zusammengebaut, validiert und auf Fehler getestet. Dann der Intel Kulim Die Sort Die Prep (KMDSDP) ist der Ort, an dem die wahre Magie geschieht. Diese Anlage verarbeitet Siliziumwafer und bereitet diese Siliziumwafer für die Chip-Vorbereitung und Kategorisierung für die Verpackung und Prüfung in Intel-Einrichtungen weltweit vor.
Wir haben das Silizium, aber was kommt danach?
Die Kulim Die Sort Die Prep (KMDSDP)-Anlage verfügt über zwei Hauptoperationen: die Vorbereitung und Sortierung der Matrizen. Heutzutage sind 300-mm-Wafer die Standardgröße, die bei Kulim hergestellt wird. Hier durchlaufen sie eine Reihe von Prozessen, die sie in einzelne Chips vereinzeln.
Wafer werden auf flexiblen Mylar-Folien befestigt und durchlaufen verschiedene Prozesse, wie etwa Schleifen und Ausdünnen auf ein exaktes Profil, um individuelle Chips zu erzeugen. Mithilfe von Vakuum und UV-Licht werden die Späne getrennt und vor dem Sortieren in Schalen gelegt. Um die Chips zu testen und zu sortieren, nutzt Intel riesige Sortiermodule, so groß wie ein Bus, mit 20 Testzellen mit einem Gewicht von je 1.000 Pfund. Es war dort so gelb, dass es sich anfühlte, als wären wir in Mexiko.
Ein speziell entwickelter Hebemechanismus, der mithilfe eines Luftkissens über dem Boden schwebt, manövriert diese Module. Die Chips werden auf Tabletts geladen und auf verschiedene Testzellen verteilt.
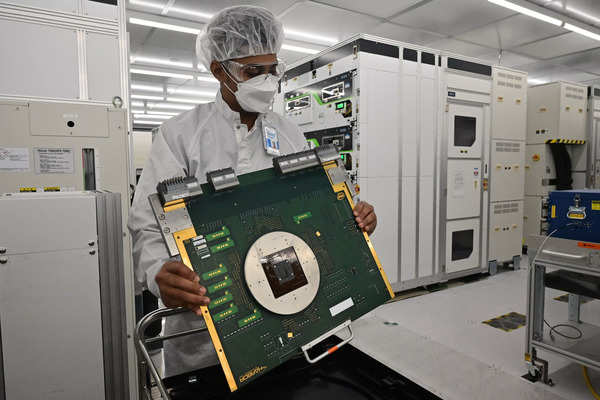
Einer der Tests besteht darin, sicherzustellen, dass die Chips zuverlässig und fehlerfrei sind. Jedes wird mit einer Prüfkarte getestet. Die Sondenkarte besteht aus Tausenden dünner Nadeln, die sogar dünner als menschliches Haar sind und mit dem integrierten Schaltkreis im Inneren des Testgeräts verbunden sind. Dies ermöglicht die Messung der Elektrizität der Chip-Schaltkreise und die Analyse eventuell vorhandener Defekte.
Dann gibt es automatisch geführte Fahrzeuge, um diese Tabletts durch die Testanlage zu transportieren.
Nachdem ein Tablett die Test- und Charakterisierungsphase durchlaufen hat, wird es in den Bereich zurückgebracht, in dem der Wafer in einzelne Chips geschnitten wurde. Die Chips, die den Test nicht bestehen, werden getrennt, weggeworfen oder recycelt. Die Schalen mit Chips, die alle Tests erfolgreich bestanden haben, werden sortiert und einer bestimmten SKU zugeordnet. Jeder Chip wird aus der Schale entnommen und zwischen zwei Folienschichten versiegelt. Die versiegelten Chips werden dann auf eine Rolle gerollt, um zur weiteren Verarbeitung zu den weltweit verteilten Montage- und Testeinrichtungen transportiert zu werden.
Intel stellt auch eigene Testgeräte her
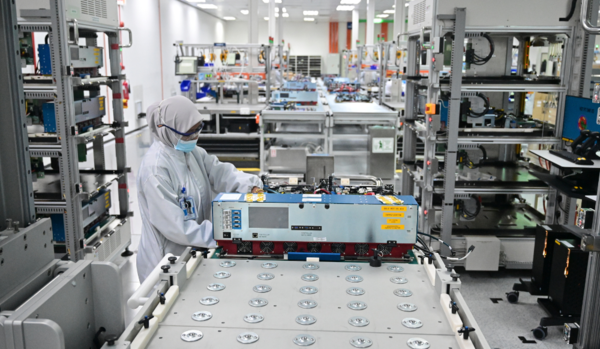
Während des Besuchs im Intel-Werk besuchten wir auch das System Integration and Manufacturing Services (SIMS)-Werk, das Testgeräte für CPUs herstellt. Zu den Maschinen, die in diesem Werk hergestellt werden, gehört auch der High-Density-Burn-In-Tester (HDBI). , der High-Density Modular Tester (HDMT)-Tester und der System Level Tester (SLT). Diese Geräte werden von Intel-Einrichtungen in Malaysia und weltweit zum Testen der CPUs verwendet.
Ein kleiner Einblick in die Testpraktiken von Intel
Eine der Montage- und Testeinrichtungen befindet sich in Penang, wo diese Chips empfangen und einer weiteren Verarbeitung und Prüfung unterzogen werden, bevor sie die OEMs erreichen. Nach Erhalt der Rollen entfernt die Einrichtung den Chip, verpackt ihn und führt Tests durch, bevor die Chips verteilt werden. Der Montage- und Testprozess von PGAT besteht aus sechs Phasen.
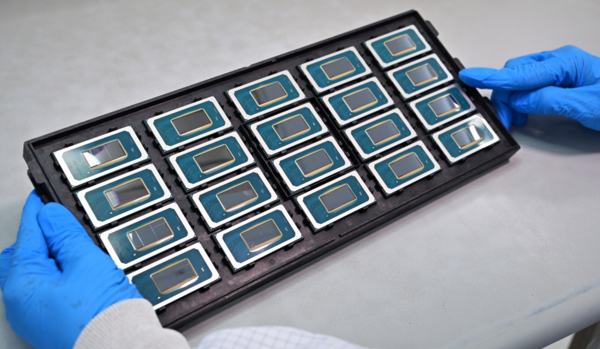
Das erste ist Chip Attach, bei dem der Chip mithilfe des Face-to-Face (F2F) Chip-on-Chip-Bonding-Verfahrens von Foveros mit dem Substrat verbunden wird. Eine zusätzliche Schicht Epoxid-Unterfüllung wird hinzugefügt, um mikroskopisch kleine Lücken zu beseitigen. Der nächste Schritt besteht darin, den integrierten Wärmeverteiler (IHS) mit Wärmeleitmaterial und Klebstoff anzubringen. Dies ermöglicht eine effiziente Wärmeableitung. Jetzt ist die CPU fertig, aber es gibt noch einen letzten Schritt, bevor sie an OEMs verschickt werden kann.
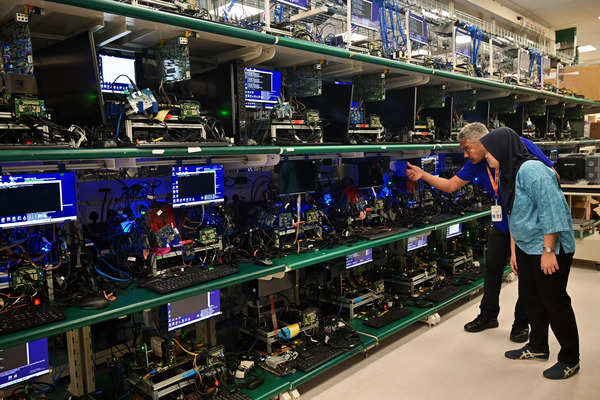
Im Design- und Entwicklungslabor in Penang wird die CPU Burn-In-, Elektro- und PPV-Tests unterzogen. Um Defekte zu erkennen, werden die Chips hohen Temperaturen und Spannungen ausgesetzt. Nach bestandener Prüfung werden alle elektrischen Leiterbahnen und Funktionen geprüft. Anschließend durchlaufen diese PPV-Tests, bei denen die Funktionalität in tatsächlichen Computersystemen des Kunden durch Simulation von Tests in kontrollierten Umgebungen bestätigt wird. Jetzt sind diese CPUs endlich bereit, in die LKWs verladen zu werden und ihren Bestimmungsort zu erreichen.