Imperial Oil and Nova Chemicals are considering plastic recycling projects in the Sarnia area.
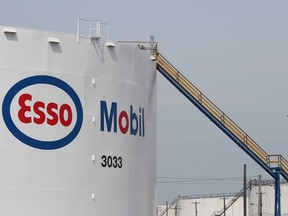
Imperial Oil and Nova Chemicals are considering plastic recycling projects in the Sarnia area.
Nova, which already operates four petrochemical production sites in St. Clair Township, said Wednesday it has an agreement with the company Plastic Energy “to explore the feasibility of developing a pyrolysis-driven advanced recycling facility” in the Sarnia region.
If built, the facility would be the largest of its kind in Canada with a potential initial capacity of 66 kiloton a year, Nova said in a news release.
“This agreement with Plastic Energy is a prime example of two companies working together to create timely, effective, and sustainable solutions that will help us make progress towards our 2030 recycled plastics ambitions, while diverting hard-to-recycle segments of plastic waste away from landfills,” said Greg DeKunder, Nova’s vice-president of circular solutions.
Recycled polyethylene manufactured using Plastic Energy-produced feedstock has identical properties to virgin polyethylene, the companies said.
Plastic Energy has two commercial recycling plants in Spain and new projects in Europe and Asia.
“We are pleased to sign this agreement with NOVA Chemicals to explore the scope for our first advanced recycling project in Canada,” said Carlos Monreal, founder and chief executive of Plastic Energy.
“We anticipate this study lasting up to eight months with a potential decision being made in mid-2024,” a Nova spokesperson said by e-mail
Imperial Oil’s Sarnia site is also being considered for one of several plastic recycling facilities its parent company, ExxonMobil, says it plans to open around the world.
If the Sarnia project receives final investment approval, the new facility would be similar to one that opened recently in Baytown, Tex.
ExxonMobil has said it plans to build facilities around the world with the capacity to process up to nearly 460,000 metric tons of plastic waste annually by the end of 2026.
“We’re considering building an advanced recycling facility at our Sarnia site,” said Kathy Porter, chemicals planning and basic chemicals manager in Sarnia.
Imperial’s Sarnia site includes a refinery, chemical plant and a research center employing about 1,000 workers.
The proposed facility would use similar technology as the ExxonMobil plastic recycling facility that opened last year in Texas, Porter said.
“It uses a proprietary technology to break down harder to recycle plastics and then transforms them into raw materials that can go into new products, such as plastics.”
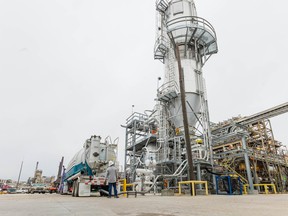
Porter said the company isn’t releasing what a recycling facility in Sarnia is expected to cost to build, the impact it would have on jobs at the site or when a final decision is expected to be made.
The Texas facility can process more than 36,000 metric tons of plastic waste a year, “which helps meet society’s objective of supporting a more circular economy from post-use plastics, and helps divert plastic waste that is currently sent to landfill,” she said.
“What we would have in Sarnia would be a similar scale and capacity as the facility in Baytown.”
Porter said the company is “trying to progress these at a slightly faster rate than our typical project planning process because there is a need for action on plastic waste.”
Many other technologies for advanced or chemical plastic recycling involve “standalone units” that can be expensive to build, Porter said.
“What we’re doing in Baytown and what we’re looking at in Sarnia actually leverages our existing manufacturing processes,” she said.
The advanced or chemical recycling proposed for the Sarnia project would see plastic waste “co-fed with other hydrocarbon material into our conversion facilities at site and the material is warmed to improve the viscosity and ultimately enters into a higher-temperature environment where that polymer molecule is broken down into smaller molecules,” Porter said.
“And then those smaller molecules are used as feed stocks to make new products, including new plastics.”
Porter said the technology is “really for the more difficult to recycle plastics that can’t be mechanically recycled,” such as home delivery pouches made up of different layers of plastic.
She said traditional mechanical plastic recycling is “really good for plastics that are one type.”
“They are basically melting down that material and then blending it in with new plastics to recycle that content,” Porter said.
One of the challenges with mechanical recycling is that when plastic has been recycled using that process a number of times, “the properties can start to be affected,” she said.
“The circular polymers that we’re making have the same quality as virgin polymers,” Porter said.
Waste plastic already collected, sorted and shredded into small plastic flakes would be trucked to the Sarnia site, she said.
“And then that material gets transferred into a large silo” and impurities removed before entering a tank where hydrocarbon material is added and warmed so that it flows, Porter said.
“And then it ultimately enters into one of our conversion units where the molecules are broken down.”
Advanced recycling technology “fits well with what folks are doing in Sarnia,” Porter said.
“It’s a project the folks on site are excited about because they can see how it makes a difference” on how “post-consumer-use plastics” are being used, she said.
“If we get more of these technologies, our end goal is that recycling is easy for folks and we’re just able to put all these materials in our blue bins” and “know that they’re getting recycled,” Porter said.
“To get there we need a lot of collaboration with industry, government, the value chain and a lot of investment on infrastructure and sorting facilities.”
Nearly 80 per cent of post-consumer plastic in Canada ends up in landfills, “mainly as a result of insufficient sorting, contamination and then the limited diversion tools at our disposal,” Porter said.
“We believe advanced recycling is a necessary complement to that traditional mechanical recycling to help address the plastic waste challenge.”
Plastics “have really changed our world,” Porter said.
Examples include reducing the weight of vehicles and improving their fuel efficiency, making windows smash resilient and improving medical treatments.
“They’re in everything and they’re critical for the safe production and preservation of food and water, and fundamentally improve the quality of our life,” Porter said.
“Plastics themselves are valuable but they should not end up in our oceans and other places in the environment, and that’s really why we need solutions to address plastic waste,” she said.
Comments
Postmedia is committed to maintaining a lively but civil forum for discussion and encourages all readers to share their views on our articles. Comments may take up to an hour for moderation before appearing on the site. We ask you to keep your comments relevant and respectful. We have enabled email notifications—you will now receive an email if you receive a reply to your comment, there is an update to a comment thread you follow or if a user you follow comments. Visit our Community Guidelines for more information and details on how to adjust your email settings.
Join the Conversation