Wooden buildings are on the rise and a St. Thomas business is bracing for its own growth, as a result.
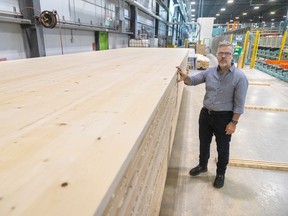
Wooden buildings are on the rise and a St. Thomas business is bracing for its own growth, as a result.
Advertisement 2
Article content
The province is about to alter the building code for mass timber towers that use all wood in construction, allowing them to go as high as 18 storeys from the current limit of 12.
Article content
Element5 on Dennis Road supplies wood panels used in mass timber construction. The more than 30 per cent increase in building height for wood towers may mean greater demand for its products, chief executive Patrick Poulin said.
“Market demand now is very strong, and with the building code and engineering methods and guidelines to allow building to 18 stores, it will boost demand. It is a tailwind for a growing market,” he said.
The Ontario government announced April 8 it is expanding the use of advanced wood construction like mass timber to help speed construction and reduce costs. Other jurisdictions such as British Columbia and in the US now allow mass timber building as high as 18 stores and it is becoming more accepted as a construction option, Poulin said.
Advertisement 3
Article content
“Big construction players and architectural firms have awareness. It is a massive market now and becoming more commonplace in the industry.”
Mass timber construction is faster and less costly than traditional building materials and has less impact on the environment than concrete. While the cost of mass timber material is higher than concrete, the cost savings is in the time to build. Wood buildings are largely built off site and assembled on site, meaning buildings can go up in a matter of weeks.
“We can design and build all components in a factory so units can be erected in a much shorter time. The costs are very favorable,” Poulin said.
Not that Element5 needs to stimulate growth. It had sales in 2023 of about $30 million and this year is forecasting $40 million with a goal of more than $100 million in 2030. It is now undergoing a plant expansion that will more than double its size to 32,500 square meters (350,000 square feet) from 13,000 square meters (140,000 square feet).
Advertisement 4
Article content
The expansion will enable Element5 to make wood beams and columns in addition to panels so it can serve more of the market.
“With the province expanding the building code, that will open up more markets,” Poulin said.
The company designs and cuts panels that become walls and ceilings and cuts out the openings for connections required for electrical or plumbing. They are flat-packed, and shipped to a construction site where they are assembled to make a building, all from wood.
Element5 began production in 2021.
In February the Austrian company the Hasslacher Group bought a stake in Element5. Now Hasslacher and private equity firm Kensington Capital Partners own Element5 but it is expected Haslacher will take full ownership, Poulin said.
Advertisement 5
Article content
“Haslacher was one of our suppliers. The fit was very good, it is good we were able to put the deal together,” he said.
“It is a capital intensive business and now we are able to grow.”
Element5 now employs about 130 and forecasts employing more than 300 by 2028.
Element5 uses mostly two-by-six sections of spruce, pine and fir. It laminates together sections as large as 16 meters long, 3.5 meters wide and 40 centimeters thick, Poulin said.
For those concerned about the fire danger and strength of wood construction, the Canadian Wood Council and the National Research Council of Canada have done extensive safety testing.
“The use of mass timber received a boost recently with the release of findings from large-scale mass timber demonstration fire tests that were led by the CWC in partnership with industry associations, federal and provincial government agencies, and fire safety and engineering consultants,” stated an article on the construction industry website Construct Connect.
Advertisement 6
Article content
“The tests solidified the use of mass timber as a safe construction material and showed that even in rare worst-case fire scenarios where sprinklers have failed and fire fighters are unable to reach a blaze, mass timber buildings perform similarly to noncombustible construction.”
Element5 has supplied materials for wooden structures across Ontario. But in London there has been little in the way of mass timber building to date and certainly no highrise developments planned, city building officials said
“There has not been a huge uptake on mass timber. Going from 12 to 18 storeys is certainly helpful, it is an option people can look at, but right now concrete is in use,” said Jared Zaifman, chief executive of the London Home Builders Association.
Advertisement 7
Article content
“I have not heard anyone talking about it. But it is another tool in the tool kit.”
The building code changes are part of a series of initiatives from the Ontario government to speed housing construction. In January and February, Ontario, British Columbia and Quebec participated in a national consultation on potential building code changes to expand the use of mass timber construction.
“I think in general any time there is flexibility in using materials it is a good thing for the industry,” said Mike Wallace, chief executive of the London Development Institute.
The construction industry contributes about 40 per cent of all global CO2 emissions. Steel and concrete produce about five per hundred each of that total. Mass timber can reduce that amount.
A 2019 study by the Yale School of the Environment found that a hybrid mass timber building achieved 26.5 per cent lower global warming potential than a concrete building.
Recommended from Editorial
Article content